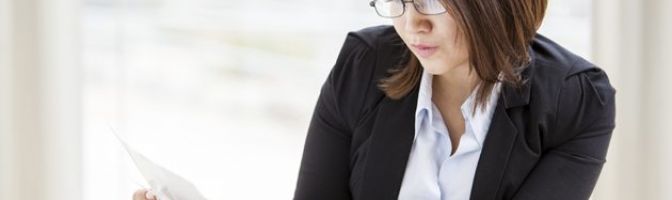
What Defines Lean Operations?
Ever since the recession forced many businesses to adjust everything from hiring practices to inventory, the term “lean operations” has been a buzzword. But what does it truly take to run lean and keep employees engaged and motivated? TheWire explains.
Defining Lean Operations
Simply put, lean operations is the practice of producing products and services using the least possible amount of inventory, supplies, time and personnel. While the concept is easy to grasp, the practice of running lean requires a comprehensive, systematic approach to minimizing excess.
Here are four tips to put your business in lean operations mode:
1. Conduct a process analysis
Create a detailed process flow diagram that fully illustrate the steps involved in creating your products or services, then eliminate or alter non-productive activities. For instance, if you accept supplier deliveries any time, consider creating one or two delivery times you can plan around. This will minimize disruptions that divert employee resources or create downtime. For tips on creating an effective process flow chart, visit wikihow.
2. Look everywhere for wasteful practices
Are quality control lapses resulting in costly product defects? Are hiring practices netting inexperienced employees who slow down the workflow? Is poor supply management resulting in production shortfalls or overruns? Whether its quality control, production or some other facet of your business, take everything into account.
3. Consider products and services from a lean perspective
Smart product design reduces material and processing requirements. Take a close look at your products to see if there are areas to improve production efficiency. If you’re too far removed from the process to judge effectively, ask employees to weigh in. Solicit their opinions and encourage efficiency brainstorming sessions. The tried and true suggestion box may also yield valuable insights from unexpected sources, such as the security guard who’s a retired engineer or the admin who’s a design student.
4. Maintain minimal inventory
Focus on maintaining a just-in-time inventory management policy that can minimize the logistics and financial burden involved in storing and handling inventory. When you consider inventory, remember to assess everything from raw materials and work in progress to finished goods. For insights into how Harley-Davidson adopted just-in-time inventory practices to compete with foreign manufacturers, check out this case study.
Motivating employees in a lean environment
While the prospect of running lean may sound ominous to employees, solid internal communication can motivate them to achieve more with fewer resources. Keep employees fully informed and involved with new lean operations from the beginning. The following tips will help you to win the cooperation of your employees:
- Re-train all your employees - Teach them about the new methods and processes and how their performance will be measured under this new paradigm.
- Create a reward system - Reward those who learn quickly and adjust to the new standards of performance. Hold regular follow-up meetings that can help everyone to improve their performance.
In most cases, running lean means less waste, lower costs and higher profits. If done correctly it also yields employees who are motivated to do more with less. Is your business ready to go lean or get leaner? It could pay to give it a try.
The trends, insights, and solutions you need to grow your business.
By signing up, you’re subscribing to our monthly email newsletter, The
Wire. You may unsubscribe at any time.
Your information stays safe with us. Learn more about our privacy
policy.